Thymly connected its new metal detector to its PLC system to keep track of run sizes, run times, line workers and product type, as well as temperature and humidity. This reduces the potential for user error and allows the operator to focus on other tasks.
Connecting the metal detector to the plant’s PLC system enables Thymly to make another productivity-enhancing advancement. Currently, when the metal detector senses a reject, the line stops and an audible bell sounds to alert the operator, who addresses the situation. Once the robotic palletizer is installed and connected to the plant’s PLC, the metal detector will send a signal to the palletizer when it senses a reject, and the palletizer will automatically divert that package to a separate area.
When a product is rejected, Thymly runs the product back through the metal detector to find out if the reject was false or valid. If it’s rejected again, the product is sent to Thymly’s quality assurance team for further investigation.
“We’ve had no problems with false rejects with the Safeline metal detector, in part because we take the time to set the machine up correctly. It’s very easy for the detector to learn a new product with its built-in auto set-up routine,” said Rahn. “The first time we see a new product, one pass through the detector’s auto set-up routine takes about three minutes. But since we’re working with such small detection pieces to achieve the highest sensitivity, we spend an extra five minutes to be sure the settings are just right. It’s very easy to use.”
After the detector learns a new product for the first time, the parameters are stored in memory. The next time that product is run, it takes less than one minute to change over the metal detector. During product changeovers at Thymly, the operator chooses the product code from the metal detector’s touchscreen control panel, and the production supervisor verifies the code is correct. With triple frequency operation, Thymly’s PowerPhasePRO RB maintains the highest sensitivity across the broadest range of products.
“We regularly test the metal detector by intentionally passing test strips through to confirm they’ll be identified,” noted Rahn. “We’re at the highest standard that you can achieve.” Thanks to this kind of attention to detail, Thymly has earned a superior rating from the American Institute of Baking and has become an SQF-certified practitioner.
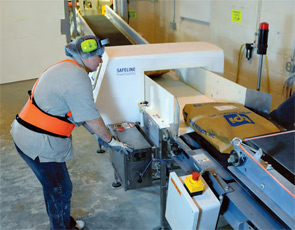
“Our dedication to achieving this high level of food safety and producing high quality product has contributed to our success,” explained Rahn. “We’ve been growing by leaps and bounds despite the economy. We’re currently one of the largest suppliers of dry ingredient blends on the East Coast, producing both Thymly-branded products and private label products. We’re now starting to go nationwide and international.”
Thymly Products found its niche over the years in incorporating specialized food ingredients into a wide variety of baked goods. Since the company was founded in 1967 by Harry Muller-Thym, it has seen four generations of the Thym family managing the business and serving its customers.
“We often find that our standard mixes and dough conditioners meet customers’ needs, but we’re happy to create a custom blend, if needed, often at no extra cost. These ingredient blends enable bakers’ mixing personnel to scale one ingredient rather than several, saving the customer both time and money,” said Rahn. “We know that the only way to grow our business is by helping customers grow their businesses. Our aim is to supply functional ingredients that exceed customers’ expectations. Assuring the highest product quality and food safety is an important part of that.”
ACCESS THE FULL VERSION OF THIS ARTICLE
To view this article and gain unlimited access to premium content on the FQ&S website, register for your FREE account. Build your profile and create a personalized experience today! Sign up is easy!
GET STARTED
Already have an account? LOGIN